Japan's secret weapon in semiconductors: mini wafer factory.
For a long time, the industry has generally believed that, due to the poor management of Japanese companies and the ineffective policies of the Japanese government, Japanese semiconductor companies are far behind the semiconductor companies represented by South Korea.
However, is the above point of view true?
Looking back at history, Japanese semiconductors indeed had a time when they dominated the world. In 1986, 37 years ago, the top three global semiconductor sales rankings were as follows: NEC, Hitachi, and Toshiba. Moreover, companies such as Fujitsu, Matsushita Electric Industrial, and Mitsubishi Electric also performed very well, and it can be said that Japanese companies were the absolute global leader at that time.
However, some "unpleasant things" happened later, such as after World War II in 1945, the Japanese aviation industry, which had created the Zero fighter, was forced to disintegrate, and the United States even led the "destroy Japan's car" campaign, and oppressed the once brilliant Japanese industrial technology (industry). For several years, the American "giant" continued to threaten Japan.
At that time, Japan did indeed pose a threat to the United States in terms of security. The reason is as follows: since semiconductors are extremely important for the production of weapons (such as missiles, etc.), if semiconductors were all produced by Japan, it would indeed pose a "security guarantee" threat to the United States.
Advertisement
The global semiconductor sales rankings in 1971 were as follows: the top one was TI (Texas Instruments), the top two were Motorola, and the top three were Fairchild Semiconductor, all of which were American companies. Because Japan surpassed the United States in just 15 years, the "Japanese threat theory" began to spread.
Although facing the control of the United States, in the global semiconductor sales rankings in 1989, the top three were still occupied by NEC, Toshiba, and Hitachi. Because Japanese companies were not "defeated", in 1991, the second semiconductor agreement was concluded between Japan and the United States.
Even the strongest Japanese companies could not resist the second suppression of the United States, and finally gave up the "throne" of the top one in global semiconductor sales in 1992 to American Intel.
On the contrary, the South Korean semiconductor industry, which was not threatened by American pressure, has developed rapidly. According to reports, in 1998, the annual sales of semiconductors in South Korea and Japan were almost equal. That is, as the United States wished, Japan's semiconductor industry was defeated!
However, Japan did not collapse because of the suppression of the United States.World-Renowned Materials and Equipment
After World War II, the United States was concerned about Japan's Zero fighter and was determined to destroy it, but Japan's aviation industry was not completely defeated. Honda Jet and Mitsubishi Space Jet (MRJ) were fortunate to survive. In the global large passenger aircraft market, Boeing from the United States and Air Bus from Europe have an overwhelming advantage. There are no Japanese companies in military applications.
However, the aforementioned passenger aircraft are equipped with many parts from Japanese manufacturers. In addition to aircraft, the contribution of Japanese companies to other manufacturing industries (such as the automotive industry) is also not to be underestimated. Japan has transferred the resources that should have been concentrated in the aviation field to other fields represented by the automotive industry, and has achieved great success.
In the semiconductor industry, Japanese companies still adopt the "support behind the scenes" policy, that is, to avoid the "dazzling" finished product market, and focus on the "behind the scenes market" such as equipment and materials.
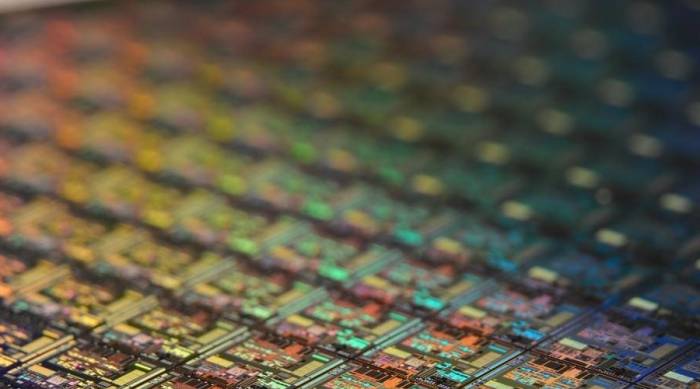
As we all know, in the field of silicon wafers, which is also the basic field of semiconductors, Shin-Etsu Chemical and SUMCO from Japan rank first and second in the industry, accounting for more than 50% of the market share. In addition, as you have seen in the news, the United States controls the export of cutting-edge semiconductor production equipment to China, and at the same time, it requires the Netherlands and Japan to keep pace with the United States. At present, cutting-edge semiconductor production equipment is monopolized by Japan, the United States, and the Netherlands. In addition, among the global TOP10 manufacturers, four are Japanese companies.
"Production equipment = operating machinery" and "parts & materials" are essential for producing semiconductor equipment.
According to the "Global Industrial Equipment Manufacturers Ranking TOP10" dated November 28, 2022, among the top 10 global industrial equipment companies, five are Japanese companies. Chinese and Korean manufacturers are also in the TOP10, but in terms of high-precision equipment, almost no manufacturers can compete with Japanese companies.
In addition, Japanese companies also perform very well in some specific fields.
For example, the market share of Japanese companies in the fields of photoresist (Photo Resist), photo mask blanks (Mask Blanks), and photo mask blank inspection equipment is almost 100%. In addition, Japanese companies also have a very strong advantage in the fields of photo masks, mask blank film (Pellicle), photo mask inspection equipment, and EUVL direction silicon wafers.
In addition, when Japan banned the export of "polyimide", "photoresist" and "high-purity hydrogen fluoride" three semiconductor materials to South Korea, it almost shocked the entire South Korean semiconductor industry.Although South Korea once advocated for domestic production, four years have passed and South Korea still cannot produce products with a purity of 99.9999999999% (12 nines). Just as Reuters reported on March 16 this year in the article "Japan Lifts Restrictions on Exports of Semiconductor Materials to South Korea, South Korea Withdraws Complaint to WTO," the Japanese government "showed a favor."
BS WORLD published an article on January 10, 2020, titled "Liquid Hydrogen Fluoride ~ Japanese Government Allows Exports After Half a Year," and pointed out that the high-purity liquid hydrogen fluoride of companies such as Morita Chemical and STEL LACHEMIFA CORPORATION has a market share of 80% to 90%.
On July 3, 2019, Reuters disclosed an article titled "Materials Restricted by Japan for Export to South Korea and Their Importance," which pointed out that Japan produces about 90% of the world's fluoropolyimide, 70% of etching gases, and 90% of photoresists.
However, Japan's advantageous materials are not limited to the above three. According to an article titled "Finally, the Era of Semiconductor Materials Has Arrived" published by the Japanese "Electronic Device Industry News" on July 7, Japanese companies provide more than half of the world's semiconductor materials.
"Miniature Wafer Factory," Help Japan Return to the Peak?
Although Japan is building a 2nm wafer factory and has a joint venture with TSMC to build a factory in Japan, many people think this is not a very effective way. For Japan's semiconductor industry, it can develop the finished product (semiconductor) industry by fully leveraging equipment and material advantages. And the power to undertake this great task comes from the "Miniature Wafer Factory."
The industry generally believes that semiconductor production requires huge investment. On the one hand, the semiconductor foundry business of companies such as Taiwan Semiconductor Manufacturing Company (TSMC) is booming in the industry; on the other hand, the continuously increasing demand has led to longer and longer semiconductor delivery periods. To solve the long delivery period and slow response speed of the semiconductor industry, the Japan Industrial Technology Research Institute (AIST) has been developing a "Miniature Wafer Factory" since 2008. The "Miniature Wafer Factory" has the characteristic of being able to produce small quantities and a variety of products, bringing a new trend to the semiconductor production industry.
The "Miniature Wafer Factory" has always been used for producing prototypes, and in order to apply it to mass production as soon as possible, the researchers of AIST established the "Hundred Semiconductors Company (headquartered in Kashiwa City, Chiba Prefecture, Japan)" in December 2022. The company name includes the meaning of "providing customers with a variety of semiconductors." Its representative director, Mr. Mura Mura, said: "We plan to create a world where everyone can design and produce semiconductors."
The advantage of the "Miniature Wafer Factory" is that it can produce any number of semiconductors, even one. Different from the large-scale production that has always been the case, its advantage lies in small quantities and a variety of products.
The "Miniature Wafer Factory" does not use traditional large wafers, but instead produces circuits on a "Half Inch Wafer" with a diameter of 12.5 cm. The size of the production equipment is 30 cm (width) * 144 cm (height) * 45 cm (depth), and this equipment can be used for exposure and many other processes, and can also be used in conjunction with the equipment of the "Mega Fab (Giant Wafer Factory)." Since the equipment used in each process is basically of similar size, robots can be used to transport wafers between each device.In addition, the "Mini Fab" is equipped with a "Minimal Shuttle" that can seal "Half Inch Wafers," thus eliminating the need for a clean room. Although it is not suitable for the production of ultra-high-end semiconductors, it is more than capable of producing sensors, micro-electromechanical systems (MEMS), and other products.
One of the advantages of the "Mini Fab" is the reduction in equipment investment. Generally, a large-scale wafer fab requires an investment of several hundred billion yen (or even more) in equipment. On the other hand, the investment target for the "Mini Fab" is 1/100 to 1/1000 of that. Since the size of various equipment is smaller, there is no need for large-scale factory land or "photo masks" for forming circuits, so the cost difference compared to large-scale wafer fabs is vast.
Furthermore, the delivery cycle of the "Mini Fab" is also extremely short. For large-scale semiconductor production, the time from production to delivery is very long; the "Mini Fab" adopts a "Just In Time" model that produces the necessary amount of products in the necessary time.
The above characteristics are most likely to play a role in the production of small quantities and a variety of semiconductors in the direction of IoT (Internet of Things). Representative Director Ikumura said, "Because the customer's order volume is small, we can respond to small orders that foundries cannot cope with."
Since the launch of the project in 2008, the National Institute for Advanced Industrial Science and Technology (AIST) has been developing production equipment and "Half Inch Wafers." At the same time, in order to promote the "Mini Fab" as soon as possible, AIST established the "Mini Fab Promotion Organization (located in Tsukuba City, Ibaraki Prefecture, Japan)" in 2017, but the progress is slow. The reason is that there is no "player" who uses the "Mini Fab" to produce semiconductors. Representative Director Ikumura clearly stated, "We have commercialized production equipment and 'Half Inch Wafers' early on, but we have not found talents and companies that can skillfully use the Mini Fab."
To further promote the "Mini Fab," "Hundred Semiconductors Company" focuses on semiconductor prototypes and orders that large wafer fabs cannot arrange. The "Mini Fab" is moving from prototyping to mass production by solving issues step by step, such as making complex business decisions (such as accurately predicting customer needs, judging the feasibility of investment, etc.). By accepting orders that giant wafer fabs cannot absorb, further promotion is achieved.
Now, "Hundred Semiconductors Company" is actively promoting semiconductor design, prototyping, and mass production activities. By sharing experiences with customers, the goal is to popularize production technology, and at the same time, continue to improve the speed of improving prototypes to move towards mass products as soon as possible.
In addition, AIST is also promoting the development of design software that can be used for the "Mini Fab." The goal is to develop a PDK (Process Design Kit) for the complementary metal-oxide-semiconductor (CMOS) direction within one year. At the same time, to make it easier to use, it is also considered to standardize the basic circuit design and apply it to the R&D direction first. In the future, the trial production will be carried out by AIST's Coastal Sub-center (Koto-ku, Tokyo) and Tsukuba Center (Tsukuba City, Ibaraki Prefecture).
In addition, AIST is also exploring new applications. For example, considering the issue of power consumption, AIST is discussing filling the needs that cannot be met by field-programmable gate arrays (FPGAs), with the goal of providing and popularizing more of the above design and process R&D services. AIST stated, "We can flexibly respond and meet customized needs."
Now, AIST has completed the development of the front-end process (circuit formation), bonding, and other processes. The goal for the next five years is to integrate the packaging substrate on the "Half Inch Wafer." Package semiconductors with a smaller area, reduce power consumption, and explore more application scenarios.To further promote the "mini-wafer fab," the General Research Institute aims to increase the production of "Half Inch Wafers" to 50,000 units per year within the next five years. In the future, not only will they have their own production base, but they will also engage in self-production. The representative director of the village pointed out: "For companies involved in the promotion organization, the mini-wafer fab is just one of their options. We will fully play the role of a leader in promoting this type of production model."
The main theme of the semiconductor industry has always been "mass production, mass consumption," but the "mini-wafer fab" can provide the required quantity to customers when necessary. On the other hand, it also faces the challenge of deepening the customer base and cultivating a customer base with multiple needs. At the same time, the General Research Institute is also striving to develop technology to provide semiconductor production and design services to a wide range of customers.
Leave A Comment