Towards the "new" track of power semiconductors.
Today, it is unimaginable for us to live without electricity. Every aspect of our lives is increasingly dependent on electrical power. In the process of electricity production, distribution, and use, power conversion plays a crucial role.
First, let's understand what power conversion is. Simply put, power conversion is the process of transforming electricity from one form to another. This conversion may involve changes in voltage, current, and frequency, making the electricity suitable for the needs of specific applications. For example, when we use televisions, refrigerators, or other electronic devices at home, the electricity we are using has been converted. These electrical appliances need to convert the alternating current supplied by the power grid into the direct current they can use. In addition, power conversion also plays a key role in the production of renewable energy sources such as wind or solar power, converting the produced electricity into a form that can be used in our daily lives.
However, every time power conversion is carried out, a portion of the energy is lost. Although this part of the energy may seem negligible, due to the continuous operation of many devices in our daily lives, these energy losses accumulate to a very large number. Therefore, improving the efficiency of power conversion is particularly important. Moreover, the improvement of power conversion technology also has a positive impact on reducing carbon emissions and protecting the environment.
The question arises, how to improve the efficiency of power conversion? This may be a complex issue in the fields of engineering and science, and methods to improve efficiency may involve design, materials, control strategies, and other aspects, including choosing the appropriate power conversion topology, using advanced semiconductor materials, using advanced algorithms to optimize control strategies, and improving heat dissipation design, etc.
Advertisement
Among the many methods, improving the materials of power devices is currently a hot topic in the industry. From the initial Si to SiC/GaN, power devices have shown a significant advantage in efficiency conversion. As the industry continues to explore more new materials, power devices will usher in greater development breakthroughs.
The evolution of power device materials
Silicon, as one of the most commonly used semiconductor materials, occupies the dominant position in the power device market. Its main advantages are abundant resources, mature process, and low cost. However, the electron mobility of this material is relatively low, and the voltage and frequency limits are also relatively limited, which restricts its use in some high-end applications.
Silicon carbide (SiC) is gradually gaining popularity in high-power and high-temperature applications with its wide bandgap characteristics. Its high voltage tolerance, low conduction loss, and good high-temperature performance give it advantages in many applications, gradually encroaching on the market share of silicon. However, the relatively high cost is a major obstacle to its popularization.
Gallium nitride (GaN) is also a wide-bandgap semiconductor material. GaN has the advantages of high electron mobility, low conduction loss, and is suitable for high-frequency applications. However, the disadvantage is that the manufacturing process is complex, and the cost is relatively high.
At present, the above-mentioned materials are mainly used to manufacture power devices on the market, but at the same time, the industry is also continuously exploring new materials. In particular, gallium oxide and diamond, these two materials are receiving more and more attention.Gallium oxide, as a relatively new semiconductor material, has a wider bandgap width (approximately 4.9eV) compared to silicon carbide and gallium nitride, and it has a theoretical critical breakdown field strength of 8MV/cm. Its high breakdown electric field and lower loss show great potential, but due to the relatively immature manufacturing process, its application is still in the exploratory stage. In the future, gallium oxide is expected to find its place in high-voltage and efficient power conversion systems.
Diamond is considered the ultimate semiconductor because its performance surpasses that of old materials (such as silicon and gallium arsenide) and new materials (such as gallium nitride and silicon carbide) in many aspects. Compared with other semiconductor materials, diamond has unique advantages:
- Extremely high thermal conductivity, excellent electrical insulation performance, and high-temperature stability: Diamond is a stable material at high temperatures, and its electrical properties do not deteriorate at temperatures over 2000°C, far exceeding other semiconductor materials.
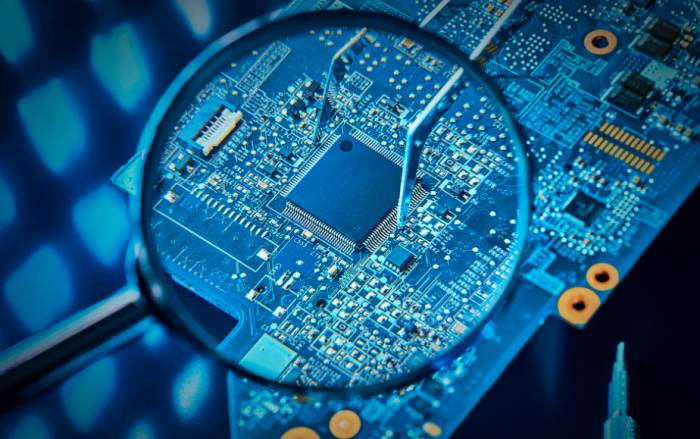
- Outstanding electrical properties: The critical electric field of diamond is 30 times higher than that of silicon and three times higher than that of silicon carbide. Unlike most semiconductors, the resistivity of diamond decreases with increasing temperature, making it excellent in high-temperature environments.
- Ultra-high current density and voltage: Compared to silicon, the current density of diamond is 5000 times higher, and the voltage is 30 times higher. This allows it to work in harsh environments of high temperature and radiation, suitable for applications under extreme conditions.
- Broad application potential: Despite the complex and costly manufacturing process, the potential of diamond in extreme environments of high temperature, high pressure, and high power is still huge. Its application range covers fields such as electric vehicles, the Internet of Things with a 20-year lifespan battery, nuclear and space applications using hardened electronic components or detectors, and ultra-precise quantum sensors for self-driving cars.
The commercialization of gallium oxide is getting closer.
In the research and development of gallium oxide, Japan is at the forefront of the times.
Masataka Higashiwaki of the National Institute of Information and Communications Technology (NICT) in Tokyo, Japan, was the first to recognize the potential of β-Ga2O3 in power switches. In 2012, his team reported the first single-crystal β-Ga2O3 transistor, which surprised the entire semiconductor device industry. The transistor they made is a device called a metal-semiconductor field-effect transistor. So, how excellent is this transistor? An important criterion for evaluating the quality of power transistors is the "breakdown voltage," which means at what voltage this device can prevent current from passing without being damaged. The transistor innovatively manufactured by Higashiwaki's team has a breakdown voltage of more than 250V, which is very excellent. In contrast, it took nearly twenty years of research and development for gallium nitride (GaN) transistors to achieve this standard.In the years that followed, many companies in Japan have been developing gallium oxide. Among them, Novel Crystal Technology (NCT), a Japanese company, is one of the earliest companies in the world to develop, manufacture, and sell gallium oxide wafers for power semiconductors. The company was established in 2015, and its technology is based on the research results of Tamura Corporation, the National Institute of Information and Communications Technology (NICT) of Japan, and Tokyo University of Agriculture and Technology in gallium oxide.
On July 28, 2023, Mitsubishi Electric Corporation, a giant in the field of power semiconductors in Japan, announced that it had invested in Novel Crystal Technology to accelerate the research and development of high-performance, low-loss gallium oxide (Ga2O3) power semiconductors, contributing to the realization of a low-carbon society. As early as 2021, Novel Crystal Technology had successfully mass-produced 4-inch gallium oxide wafers and began to supply them. Last year, the company planned to invest about 2 billion yen to add equipment to its factory, and by 2025, it aimed to build a production line with an annual output of 20,000 4-inch gallium oxide wafers. Moreover, the company plans to supply 6-inch wafers in 2023.
Mitsubishi Electric hopes to combine its long-accumulated technology for designing and manufacturing low-power loss, high-reliability power semiconductors with the gallium oxide wafer manufacturing technology of Novel Crystal Technology to accelerate the development of outstanding energy-saving gallium oxide power semiconductors.
Many challenges of diamond are being overcome.
As mentioned above, diamond is a promising material for the semiconductor industry, but to become an industrial reality, many obstacles still need to be overcome.
(1) Wafer cutting: Due to the lack of effective technology to cut diamond into thin wafers, its application is limited. Wafers must be synthesized one by one, which makes the manufacturing cost too high for most industries.
Now, a Japanese research team led by Professor Hirofumi Hidai of the Graduate School of Engineering at Chiba University has found a way to cut into thin wafers. This laser-based cutting technology is used to neatly cut diamond along the best crystal plane, thereby manufacturing smooth wafers. To prevent unnecessary cracks from propagating along the lattice, researchers have developed a processing technology that focuses short laser pulses on a narrow conical volume within the material. Professor Hidai explained: "The focused laser irradiation will transform the diamond into amorphous carbon with a density lower than that of diamond. Therefore, the area changed by the laser pulse will have a reduced density and crack formation."
Diamond slicing can produce high-quality wafers at low cost, which is essential for manufacturing diamond semiconductor devices. Therefore, this research brings us closer to realizing various applications of diamond semiconductors in society, such as improving the power conversion efficiency of electric vehicles and trains.
(2) Epitaxial wafers: Among all the industrial processes required for manufacturing diamond devices, the growth of epitaxial layers is one of the most critical processes, as most of the electrical performance depends on the quality of these active layers.
A French startup called Diamfab is researching the production of diamond epitaxial wafers. Diamfab is affiliated with the French National Center for Scientific Research (CNRS). The wide bandgap semiconductor team (SC2G) of CNRS has been committed to developing high-quality synthetic diamond for challenging electronic application fields for 30 years.Diamfab produces diamonds using methane, a gas that can be produced naturally and biologically without resource limitations. Two processes are used to synthesize it: HPHT (high pressure high temperature) or MPCVD (microwave plasma chemical vapor deposition).
By synthesizing and doping diamond epitaxial layers with unique control, they have developed IP for synthesizing and doping diamond epitaxial layers using plasma generated by microwaves under controlled temperature and pressure conditions. This breaks down methane molecules into carbon, which then rearranges on the surface of diamond seeds. At the same time, precise and controlled amounts of boron or nitrogen are added to grow diamond-doped layers and form high-value wafers ready for device manufacturing. As a result, stacks of diamond-doped layers are grown to form high-value wafers prepared for device manufacturing.
Diamfab is targeting the application of diamonds in the electric vehicle market. In automotive applications, Diamfab wafers can manufacture power converters that are 80% lighter and more compact in structure. In power grid applications, compared to silicon, wafers can also handle higher voltages more easily and reduce energy loss by 10 times. Diamfab said it expects all electric vehicles to adopt diamond materials within ten years.
In addition, the advancement of chemical vapor deposition (CVD) technology has also greatly accelerated the development of diamonds, which is expected to achieve 4-inch diamond wafers. Diamfab is increasingly seeing opportunities for diamond development, and they have a clear roadmap to achieve 4-inch wafers by 2025 as a key driver for mass production. The goal is to increase production in the next five to seven years.
(III) Device Development: Orbray Co., Ltd., headquartered in Tokyo, and MIRISE Technologies Corp, an automotive semiconductor research company located in Nanshan, Aichi Prefecture, Japan, have begun to cooperate in developing technology needed for the deployment of vertical diamond power devices in various electric vehicles in the future.
In the research cooperation, Orbray will be responsible for developing p-type conductive diamond substrates, while MIRISE will be responsible for developing high-voltage operating device structures to verify the feasibility of vertical diamond power devices. It is reported that earlier this year, Professor Kazuki Yosda of Saga University in Japan and Orbray developed a power semiconductor made of diamond with a working power of 875 megawatts per square centimeter, which is the highest output power value of semiconductors in the world.
Conclusion
From silicon to diamond, different semiconductor materials each demonstrate unique performance and advantages, driving continuous technological progress and providing strong support for building a low-carbon future. The continuous evolution and innovation of these materials are precisely to meet the growing global demand for energy efficiency and sustainable development. At the same time, the competition surrounding power devices is also about to enter a new track, so domestic semiconductor manufacturers need to accelerate their research and development in these advanced semiconductor material fields.
Leave A Comment